Warehouses have been around since the days of ancient Egypt, but the warehousing industry has never stayed frozen in time. Every decade brings new innovations and solutions to the warehousing industry, like computerized warehouse management systems replacing handwritten logs. But what’s next? Warehouse robotics is the next wave
Today, autonomous warehouse robots are at the forefront of the innovation discussion. But while robots are still too expensive and cumbersome for widespread use, recent advances in technology could make them a more viable solution.
What Is Warehouse Robotics?
Warehouse robots are machines designed to replicate the work of humans. Typically, they’re meant to accomplish a task that’s dangerous or repetitive. For example, instead of a human bending or stretching to reach a heavy item, a warehouse robot can lift the object without causing a human worker physical strain.
What kind of tasks can warehouse robotics accomplish?
New advances in warehouse robotics make the machines “autonomous,” or able to perform tasks independently. Whereas, in the past, most warehouse robots were designed to serve a single task. But, newer models are multipurpose and adaptable to a variety of different roles.
Some of the tasks an autonomous warehouse robot can perform in a warehouse include the following.
- Picking. Systems called Automated Storage & Retrieval Systems (AS/RS) can travel on fixed tracks to retrieve items from shelves automatically.
- Transport. Autonomous Mobile Robots (AMR) can navigate independently through a warehouse – no preset routes or rails required. This allows them to transport items from one end of a warehouse to another without breaking a sweat.
- Packaging. Robots can use arms or grippers to place items inside a package. Some may even be able to automatically calculate which box size they should choose.
- Loading & unloading. Some robots can load trucks for delivery, or automatically unload palettes and place them on warehouse shelves.
- Organizing. Conveyor belt systems can automatically sort items into different categories and deliver them to the appropriate warehouse sections.
Warehouse automation statistics
The warehouse robotics industry is expanding as more and more warehouse owners take advantage of new technology trends.
In 2019, the total warehouse automation market was worth approximately 15 billion dollars. Subsequently, in 2023, it’s worth more than 23 billion dollars and is only expected to grow further to a projected 41 billion dollars in 2027.
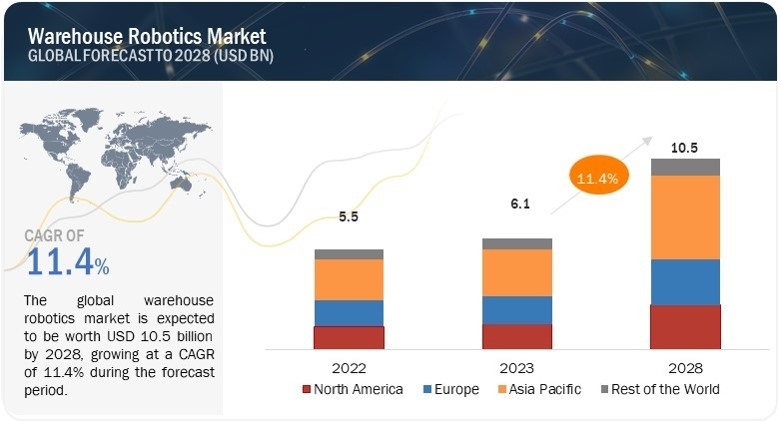
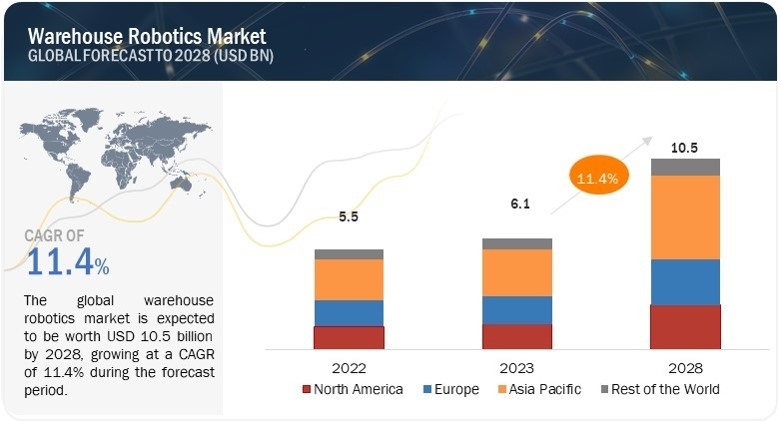
What are the potential benefits of warehouse automation?
Depending on the type of automated systems your warehouse implements, potential benefits may include the following.
- Improved worker safety. Robots can engage in tasks that are potentially dangerous for human workers, such as lifting heavy objects from high shelves. This could help lower the risk of potential accidents and workplace injuries.
- Higher productivity. Robots don’t need to take as many breaks as human workers, allowing them to operate for longer hours during the day.
- Faster picking. Warehouse robots can move faster than a human, allowing them to retrieve more items within a smaller time window.
- Fewer errors. Robots aren’t subject to human errors, such as picking the wrong item. This could lead to fewer overall mistakes and streamline your picking process.
- Optimizing warehouse space. Using warehouse robots may allow you to place shelves closer together since they can enter smaller spaces that humans can’t. This allows you to increase your maximum storage capacity and optimize your warehouse layout.
Potential cons of warehouse robotics
Of course, warehouse robots aren’t without their hurdles. For instance, many barriers still prevent the more widespread adoption of automated warehouse technology, including the following.
- Cost. Warehouse robotics technology still falls on the expensive side. A fully automated warehouse can cost over 30 million dollars, depending on the size of the warehouse and the cost of individual robots. Even a semi-automated warehouse can cost between 5 to 15 million dollars, which may keep smaller or more budget-conscious warehouse owners from making the leap.
- Maintenance. Robots will still need long-term maintenance and upkeep to operate correctly. If a crucial warehouse robot malfunctions, warehouse operations may come to a halt.
- Staff training. While robots may cut back on more general warehouse work, you’ll still need to train staff to work side-by-side with the automated systems. You’ll also need personnel to maintain or repair the robots, which can be expensive.
- Less adaptability. While many robots can perform multiple tasks, other systems are designed to be used only within a certain context. If your warehouse layout or internal operations should change, the warehouse robots may need to be replaced.
Warehouse automation examples for the real world
Instead of fully automating a warehouse, many warehouse owners or managers may decide to start small with a “trial run.” For instance, implementing an automated picking system that retrieves items and delivers them to a centralized “hub.” Then, human workers can physically pack the retrieved items into packages.
The robot can travel across the warehouse with ease, preventing human workers from walking long distances every day. Furthermore, this hybrid approach can combine the best of both worlds, allowing you to take advantage of a robot’s efficiency without replacing the human element. Many warehouses may ultimately find this approach preferable to full automation in the long term.
Conclusion: Warehouses in robotics
Undoubtedly, the warehouse automation market is on track to pass 40 billion dollars in 2027. Thanks to new advancements in the industry, like multipurpose robots, we’ll likely see more automated systems implemented in warehouses in the coming years. However, barriers like the high upfront cost and maintenance mean that many warehouses will prefer a hybrid approach of both human workers and automated systems.
Want to work with a Rhode Island warehouse that keeps up with the latest trends in warehouse technology? Contact N&D Transportation Company today to learn more about working with us.