Modern warehousing practices and methods have evolved rapidly within the last decade. Subsequently, while it’s easy to get caught up in cutting-edge developments, like AI and automation, it’s also easy to forget the basic principles that form the foundation for success.
The concept of warehouse management is as old as warehousing itself, and several time-tested practices have endured in successful warehouses across the globe. Therefore, if you’re new to running your own warehouse, find a quick guide to modern warehousing practices and methods below. But even if you’ve been in the business for years, it never hurts to refresh yourself on the importance of warehouse management.
What is warehouse management?
Warehouse management is the strategic art of controlling your warehouse or distribution center’s resources, including the physical storage space, inventory, and employees.
The goal of warehouse management is to optimize the flow of your day-to-day operations and help it run as smoothly as possible. Warehouse management pre-dates the digital age. Nevertheless, modern warehousing practices and methods can give your business a whole new edge.
Modern warehousing practices for efficiency and organization
Modern warehousing practices track inventory digitally
The days of tracking inventory with handwritten or typed records are a thing of the past. Manual systems can be rife with mistakes and input errors. So, it’s better to rely on the help of a warehouse management system (WMS)
What is a warehouse management system, you might ask? In modern warehouses, it’s an application that digitally tracks your inventory and manages other aspects of your day-to-day operations. A WMS can use barcodes or RFID scanners to allow employees to automatically enter new inventory into the system, helping you keep tabs on everything within your warehouse walls.
Choose the right picking method
Depending on the size and nature of your inventory, the most efficient picking method for your warehouse can vary. Some of the most common methods include:
- Batch picking: Firstly, this picking method has an employee pick multiple orders in a single batch as they move throughout the warehouse. Combining orders together helps reduce travel time, potentially boosting efficiency.
- Zone picking: Secondly, with this method, you’ll assign a specific picking zone to individual employees. Each employee will stay in their designated section instead of crossing the warehouse for different items This method prevents internal “traffic jams” in warehouse corridors.
- Wave picking: Lastly, this picking method divides orders into “waves” with similar characteristics, like those with a similar product type or destination. Employees will work to complete each wave of orders within a set time period, then start a new wave once they’re complete.
Go back to your “ABCs”
A well-optimized layout can minimize the time your employees spend packing orders. So, when maximizing your warehouse layout for efficiency, it can be helpful to implement an “ABC analysis” of your inventory. “A” products represent your most popular items, while “C” items represent the least in-demand or least chosen items.
Your “A” items will be grouped closest to the packing area, while “B” and “C” items are further out. To help visualize the most efficient use of your current space, try using an online warehouse layout planner, like SmartDraw or Icograms.
Re-evaluate your inventory priorities
While you’re taking stock of your current layout, consider if your current inventory could use optimization. For example, are you cluttering your storage space with over-stocked items, or consistently running out of a popular item? Keep track of any fluctuations in your regular inventory demand, and adjust your re-orders accordingly.
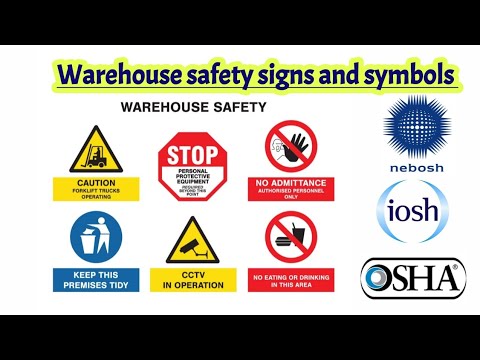
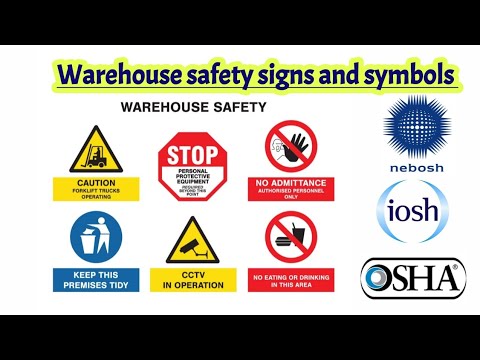
Prioritize warehouse safety as a benchmark for modern warehousing practices
A safe warehouse is also a productive one. So, whenever you refresh your warehouse’s layout or operations, always ensure that proper safety regulations are being followed.
A handful of common warehouse safety guidelines from the OHSA include the following.
- Install upright guards on vertical inventory racks to prevent forklift accidents
- Train your employees on up-to-date safety protocols and ensure that they know the locations of any potentially dangerous materials.
- Ensure that potentially hazardous materials, like flammable chemicals, are stored in structurally appropriate buildings with fire protection systems.
- Maximize your layout to prevent back injuries. For example, raise cases weighing over 35 pounds to a higher shelf, so that an employee can lift it between the knees and mid-chest.
Keep an eye on your KPIs
In order to keep improving your operations, tracking your Key Performance Indicators (KPIs) can help you understand how your warehouse performs on a regular basis. Common KPIs to track in warehousing include your:
- Order Fulfillment Rate
- Inventory Turnover rate
- Labor Productivity rate
- Average cycle time
Open yourself to feedback
Data can tell you part of the story, but the people who work in your warehouse every day can help you fill in the gaps. Open yourself to feedback and ideas from people throughout your pipeline, so you can gain a new perspective and find solutions that you may not have discovered otherwise.
Warehousing is an ever-changing field. So, there’s almost always something you can improve at every step of the process. By following good warehouse management practices and constantly seeking to improve, you can help streamline your supply chain and keep your business running right on track.
Outsource to a Rhode Island warehouse for your modern warehousing practices
Managing your own warehouse day-to-day can be quite an endeavor. Nonethless, if you’d prefer to work with a third party logistics provider who can handle the hard part for you, N&D Transportation is ready to help.
Our 12-acre North Smithfield distribution warehouse in Rhode Island contains plenty of racked, and heated storage space. We’ll keep your products safe and sound for as long as you need them, so you can devote your time and resources to keeping the rest of your business running smoothly.
Contact us today for more information about how we can meet your warehousing needs.